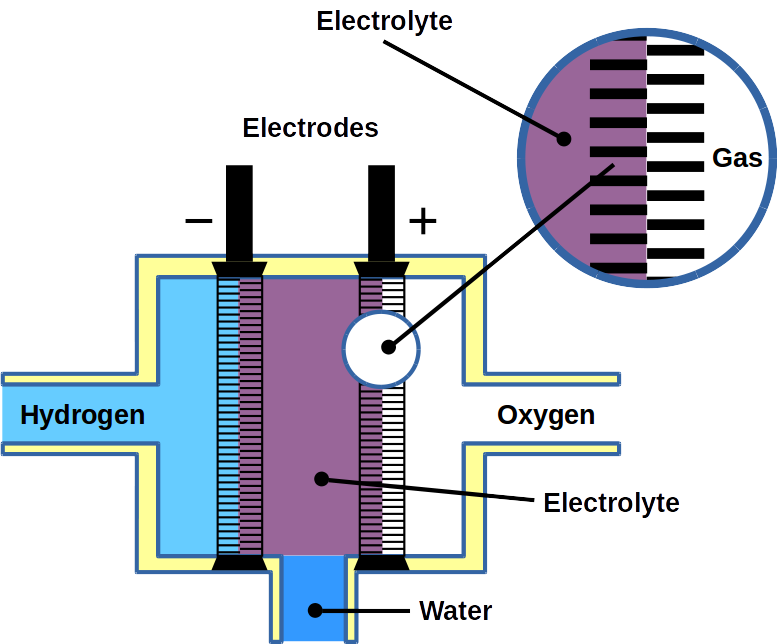
Energy-converting devices such as fuel cells are among the most efficient and clean alternative energy-producing sources. They have the potential to replace fossil-fuel-based power generators. More specifically, proton exchange membrane fuel cells (PEMFCs) are promising energy conversion devices for residential, transportation and portable applications owing to their high power density and efficiency at low operating temperatures (ca. 60–80 °C). For the complete approach, with electrolytic hydrogen renewable sources, PEM fuel cells can become one of the cleanest energy carriers. This is because water is the final product of such energy conversion systems. Currently, Nafion™ membranes are regularly used as hydrogen barriers in these fuel cells.
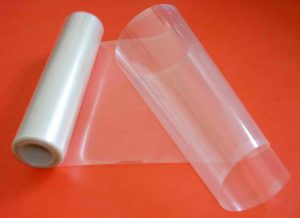
Sufficient hydrogen gas supply is crucial for practical application of the PEMFC systems. Currently, expensive high-pressure tanks (70 MPa) are state-of-the-art for hydrogen storage. Besides cost, there are other drawbacks such as portability and safety. In order to address these issues, alternative hydrogen storage materials have been extensively investigated. For example, metal hydrides and organic hydride materials, can fix and release hydrogen via covalent bonding.
Now, Dr. Junpei Miyake and colleagues of the University of Yamanashi, Japan, have proposed an “all-polymer” rechargeable PEMFC system (RCFC). The work has been published in Nature Communications Chemistry. Their strategy was to apply a hydrogen-storage polymer (HSP) sheet (a solid-state organic hydride) as a hydrogen-storage medium inside the fuel cell. With this approach, the issues like toxicity, flammability and volatility as well as concerns related to other components such as the fuel reservoir, feed pump and vaporizer were solved. The HSP structure is based on fluorenol/fluorenone groups that take over hydrogen-storage functionality.
In order to test the performance of their HSP-based rechargeable fuel cell, the scientists attached the HSP sheet of the membrane electrode to the catalyst layer of the anode. At the same time, the cathode side was operated as in a regular PEMFC. The researchers reported that an iridium catalyst has been applied to the inside of the HSP sheet to improve the hydrogen-releasing and fixing processes.
Fuel cell operation, cycle performance and durability were tested using cycles of 6 periodic steps. At first, hydrogen was infused into HSP sheet for 2 h, followed by nitrogen gas flushing to remove hydrogen from the anode. Then, heating of the cell up to 80°C to initiated hydrogen release from the HSP sheet. Together with oxygen gas supplied to the cathode side the fuel cell produced constant electrical current.
The team demonstrated that their HSP sheet released 20%, 33%, 51%, or 96% of the total fixed hydrogen gas in 20, 30, 60, or 360 min, respectively. The temperature was 80°C in the presence of the iridium catalyst. Also, the iridium catalyst could absorb up to 58 mol% hydrogen, which was considerably lower than that stored in the HSP. The maximum operation time was approximately 10.2 s / mgHSP (ca. 509 s for 50 mg of HSP) at a constant current density of 1 mA / cm2. The RCFCs reached cycleability of least 50 cycles. In addition, the utilization of a gas impermeable sulfonated poly-phenylene membrane (SPP-QP, another type of PEM) turned out to be a good strategy to enhance the opration time of the RCFC.
The advantageous features of the reported RCFC system include better safety, easier handling and lower weight. These are perfect for example in mobile application such as fuel cell vehicles. However, for the improvement of the RCFC performance, hydrogen storage capacity and kinetics (H2-releasing/fixing reactions) as well as catalyst stability need further improvements.