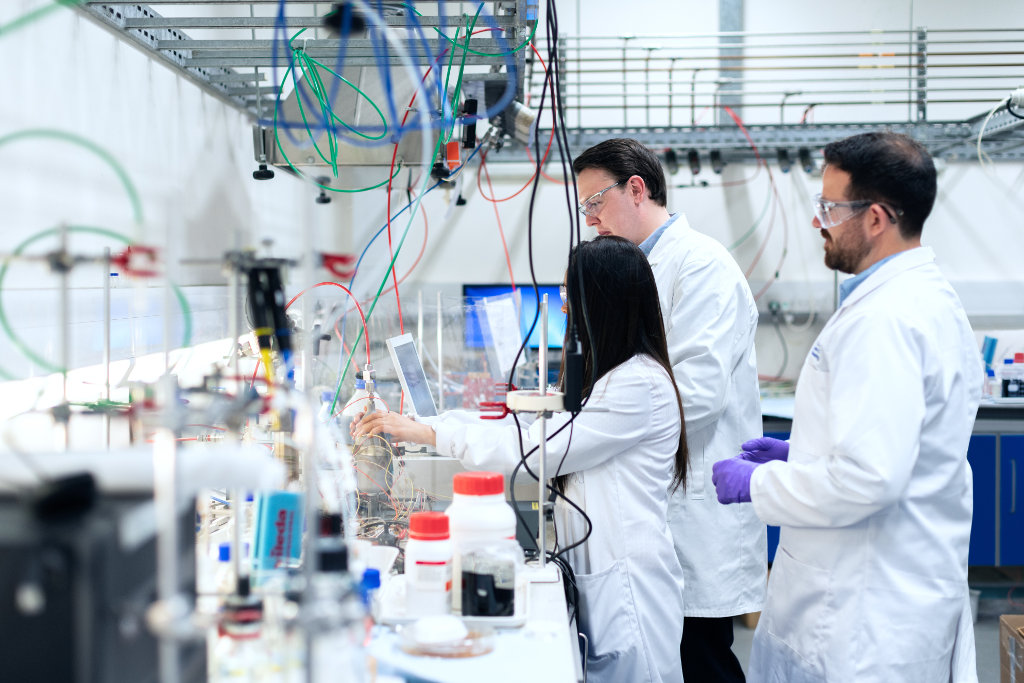
To decrease the consumption of fossil fuel-derived energy for transportation, proton exchange membrane fuel cells (PEMFCs) are one of the most promising clean power sources. Their performance, however, strongly depends on the efficiency and durability of the electrocatalyst used for the hydrogen and oxygen reactions occurring at the electrodes. Noble metals such as platinum and gold are still considered as the most efficient catalysts. At the same time, their high cost and scarcity are major road blocks for scale commercialization of these energy devices.
Various solutions of catalyst design are intensively investigated in order to make this technology economically successful. Searching for high catalyst activity and durability for fuel cells is in focus of current research and development. To date, state-of-the-art electrocatalysts are based on carbon materials with varying platinum loadings.
Ultra-high active platinum group metal (PGM) alloy catalyst
Although, recent research reported ultra-high activity of some metal alloy catalysts, problems still remain. Some of these issues are related to utilization of high atomic percentages of PGM (sometimes up to 75% Pt), poor durability and performance under industrial conditions. In search for new solutions, researchers of the State University of New York at Binghamton, USA, and their collaborators reported a new design in journal Nature Communication: a highly-durable alloy catalyst was obtained by alloying platinum and palladium at less than 50% with 3d-transition metals (Cu, Ni or Co) in ternary compositions.
They addressed the problem of severe de-alloying of conventional alloy catalysts under the operating conditions, resulting in declining performance. For the first time, dynamic re-alloying as a way to self-healing catalysts under realistic operating conditions has been demonstrated to improve fuel cell durability.
Alloy combination and composition
The wet-chemical method was used for synthesis of Pt20PdnCu80−n alloy nanoparticles with the desired platinum, palladium and copper percentages. The selected set of ternary alloy nanoparticles with tunable alloy combinations and compositions, contained a total content of platinum and palladium of less than 50%, keeping it lower than current PGM-based alloy catalysts. The incorporation of palladium into platinum nanomaterials enabled a lower degree of de-alloying and therefore better stability. Additionally, palladium is a good metal partner to platinum due to their catalytic synergy and their resistance to acid corrosion.
To reduce the need for platinum and palladium core catalysts, a third, non-noble transition metal played a central role in the catalytic synergy of alloying formation. Non-noble metals such as copper, cobalt, nickel or similar were used. The platinum-palladium alloy with base metals allowed the researchers to fine tune the thermodynamic stability of the catalysts.
Morphology and phase structure
The thermochemical treatment of carbon-supported nanoparticles was crucial for the structural optimization. The metal atoms in the catalytic nanoparticles were loosely packed with an expanded lattice constant. The oxidative and reductive treatments of the platinum-palladium alloy (PGM <50%) allowed a thermodynamically stable state in terms of alloying, re-alloying and lattice strains. The re-alloying process not only homogenized the inhomogeneous composition by inter-diffusion upon calcination of nanoparticles, but also provided an effective pathway for self-healing following de-alloying.
Single face-centered cubic type structures were observed in Pt20PdnCu80–n nanoparticles (n = 20, 40, 60, 80) nanoalloys. Copper-doping of platinum-palladium alloys reduced the lattice constant effectively, as shown by high energy X-ray diffraction. Maximized compressive strain and maximized activity of the Pt20Pd20Cu60 catalyst confirmed strong correlation between the lattice constants and the oxygen reduction activity.
The researchers demonstrated that the thermodynamically-stable Pt20Pd20Cu60/C catalyst exhibited not only the largest compressive strain after 20,000 cycles, but also high activity and high durability. The discovery that the alloy catalyst remains alloyed under fuel cell operating condition is in sharp contrast to the fully de-alloyed or phase-segregated platinum skin or platinum shell catalysts reported in almost all current literature.
The significance in understanding of the thermodynamic stability of the catalyst system is a potential paradigm shift of design, preparation, and processing of alloy electrocatalysts.
(Photo: Pixabay)