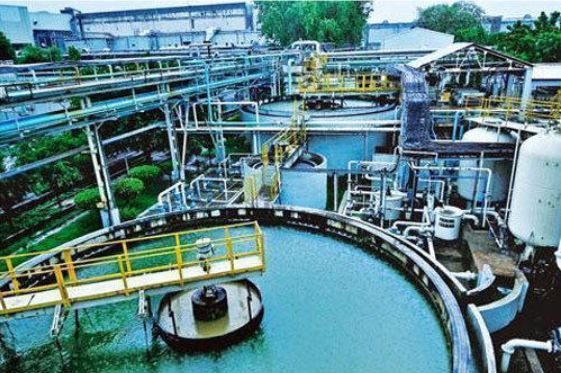
Solid oxide fuel cells (SOFCs) are highly efficient energy conversion devices and have low operating costs. They work at a temperature range of 800 to 1,000 degrees Celsius. This allows for the possibility of using internal conversion of hydrocarbon fuels into hydrogen. Methane, methanol, petroleum, and other hydrocarbons can be converted to hydrogen (H2) directly within the fuel cell.
SOFCs have a number of additional advantages over traditional combustion engines or other types of fuel cells. For example, the high exhaust heat (over 800 degrees Celsius) makes them a useful application in the industry for cogeneration of electricity and heat. Because of combined cycles, high efficiency for electricity production can be achieved. In addition, due to the modular nature of SOFCs, they offer flexible planning of power generation capacity. This way, the use of SOFCs results in a further reduction of carbon dioxide emission.
The greatest advantage of SOFCs is that they can be operated with hydrocarbon fuels such as methane (CH4, the main component of natural gas). The direct use of methane eliminates the need for pre-reformers, thus reducing the complexity, size, and cost of the overall SOFC system.
Methane can be recovered from the decay of organic waste in municipal solid waste landfills, drinking water treatment plants, etc. The gas can also be recovered from groundwater because of the naturally occurring anaerobic degradation of organic matter in the subsurface or the infiltration of methane from natural gas reservoirs.
A research team from the Delft University of Technology assumed that the gas collected from groundwater treatment can be effectively used as fuel in SOFCs and put their hypothesis to a test. They published their results in the journal Journal of Cleaner Production. Currently, the methane recovered from the Drinking Water Treatment Plant (DWTP) of Spannenburg, Netherlands is either released into the atmosphere or flared, wasting a precious resource and contributing to further greenhouse emission in the form of CO2.
SOFCs provide the cleanest of the viable solutions of converting recovered methane into electrical energy, which, in turn, can be utilized by the DWTP. This process will decrease the power demands and simultaneously reduce the greenhouse gas emissions of the DWTP.
The entire process was divided into the following steps:
- Methane was recovered from groundwater: The groundwater was pumped from the deep-wells directly to a system of vacuum towers, which remove 90% of the dissolved gas using a near vacuum of 0.2 bar.
- Subsequent treatment by plate aeration was done to remove the remaining 10% of methane in the groundwater.
- Tower aeration used to further remove CO2 before pellet softening process to lower hardness.
Recovered gas sampling:
200 mL of the recovered gas enriched in methane was used to determine the concentration of CH4, H2, Oxygen (O2), nitrogen (N2), carbon monoxide (CO), and CO2.
SOFC set up & thermodynamic approach:
A SOFC test station was used to carry out the experiments. The methane rich gas was fed to the anode and the open circuit potential was logged. Methane must be reformed to hydrogen and CO before electricity can effectively be generated in an SOFC.
Results:
The main components in the sampled gas were methane and CO2 with concentrations of 71 and 23 mol%, respectively. Additionally, the recovered gas contained 9 ppm of hydrogen sulphide (H2S), which can permanently reduce the cell performance of an SOFC. Hydrogen sulphide was effectively removed (<0.1 ppm) with impregnated activated carbon
The use of CH4 recovered from the groundwater in an SOFC helps to mitigate the greenhouse gas emissions and improve the sustainability of DWTPs. The recovered methane gas of the Spannenburg DWTP can be used to run a 915 kW SOFC system. This can supply 51.2% of the total electrical power demand of the plant and decreases greenhouse gas emissions by 17.6%, which is around 1794 tons of CO2.
The annual power generation of the SOFC system can be 8 GWh, which is about 3 GWh more than that produced by an internal combustion engine such as a gas turbine or piston engine.
In the future, the researchers will conduct a long-term tests to determine the safe operating condition of SOFC with respect to the carbon deposition issue. These tests will be extended to the SOFC stack level and pilot plant (in the range of a few kW systems)
(Photo: Indiamart)
Reference: https://doi.org/10.1016/j.jclepro.2021.125877 (A solid oxide fuel cell fueled by methane recovered from groundwater, 2021)